

Keeping you up to date on Bespoke's ongoing success story.
27 July 2021
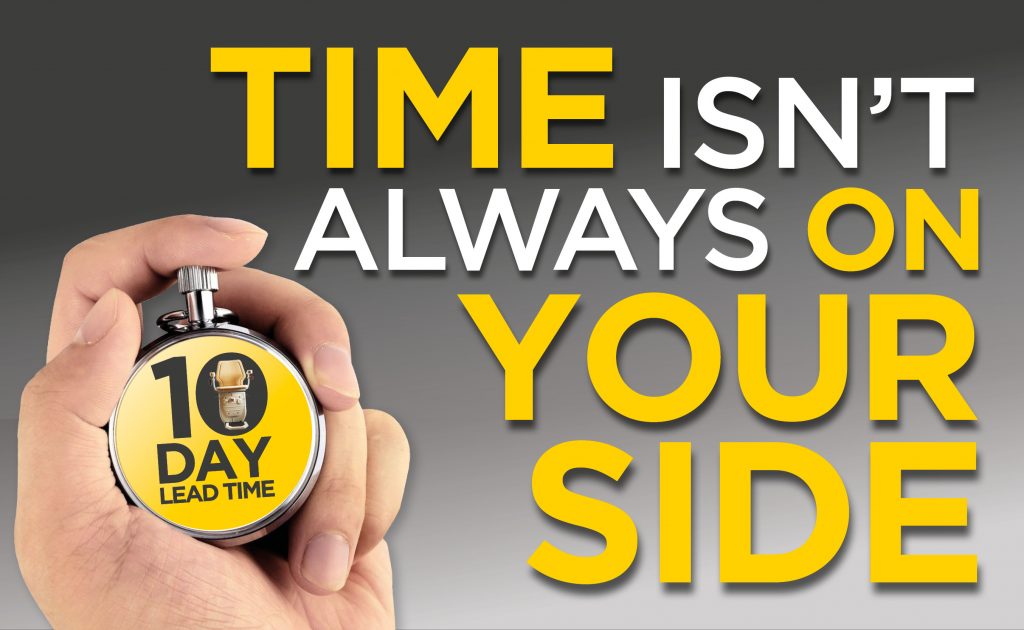
Leading the way completing and dispatching orders for dealers in days not weeks.
21 July 2021

Allowing for a wider range of installation positions and a consistent charge.
01 June 2021

One-to-one live training and demonstrations are now available, at your convenience.
29 January 2021
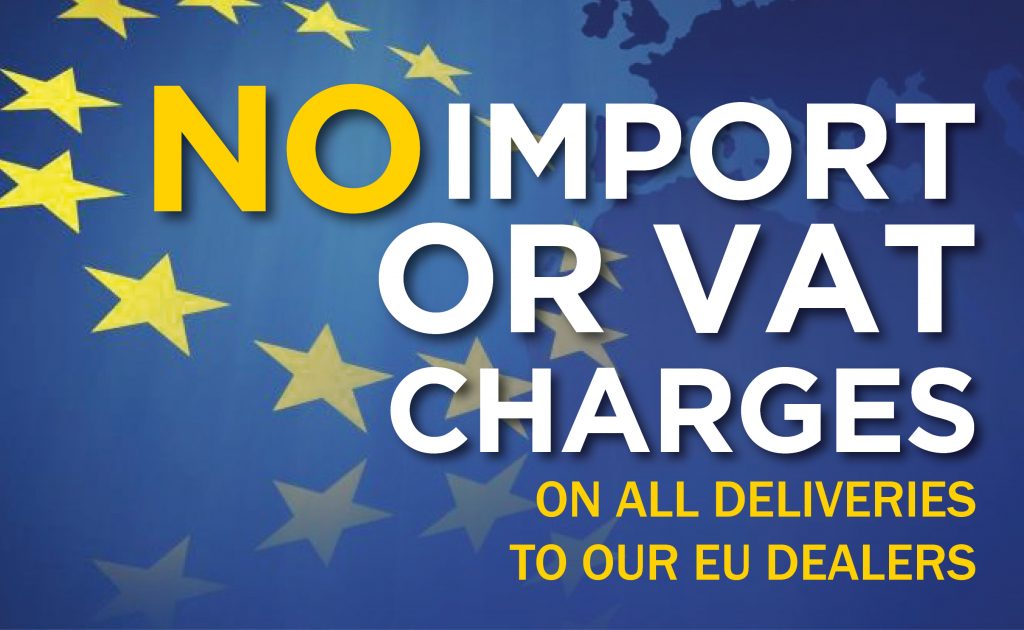
Compared to our competitors, all Bespoke EU dealers won’t have to pay VAT upon delivery thanks to our logistics.
18 November 2020

With the departure from the EU, the United Kingdom our current, and future dealers will require to provide a EORI number.
03 November 2020

Making staircase surveys, quick and easy without the paperwork and headache.
20 October 2020

A recent Bespoke installation in Switzerland maybe leading into the World Records book.
06 October 2020

We had the pleasure of visiting and training Bespoke’s latest dealers, Love Stairlifts, in Liverpool.
05 August 2020

Nearly doubling supply of the Bespoke Synergy Straight has ensured that our suppliers are getting additional work and economical gain.
21 July 2020

What goes into the production of the Bespoke Infinity Curved stairlift and rail.
15 July 2020

With an ongoing partnership with our freight providers means we can stay on track on all deliveries far and wide.
08 July 2020

Over the past few months, there has been a disruption in global businesses, at Bespoke, we’ve continued onwards.